The Missing Links in the Supply Chain
Trying to track that package? With the holidays approaching, buying and selling goods has become increasingly complicated as the global supply chain strains under the demands and limitations of the pandemic. We asked Yale SOM Prof. Sang Kim, an operations expert who specializes in supply-chain management, to unpack the news about delayed shipments and backed-up ports.
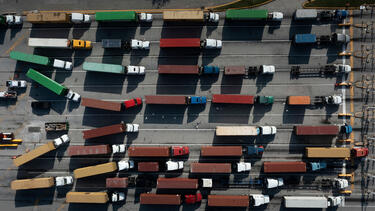
Trucks carrying shipping containers at the Port of Baltimore in October 2021.
What should holiday shoppers understand about the supply-chain jam?
For many shoppers, this holiday season will be a frustrating one because of limited selections and high prices, driven by supply-chain issues. As reported daily in the news media, we are witnessing unprecedented delays and shortages of not just consumer items for the holiday season, but just about everything.
As much as this is a stressful experience to many, one silver lining is that now everyone gets a chance to learn a lesson on how supply chains function and how fragile they can be. Before the pandemic, consumers had gotten used to the idea of one-day shipments as companies like Amazon gradually expanded their distribution network and innovated around customer services. This shielded consumers from the complexities behind the scenes, giving a false sense that products are available all the time.
“Since most supply chains are optimized for efficiency, errors are magnified in today’s globalized supply chains. The bottleneck is emblematic of what can go wrong if a carefully choreographed system is stretched beyond its capacity.”
The truth is, much about supply chains is like fine-tuned musical instruments in an orchestra: an off-pitch note here and there can be overlooked, but a prolonged misplay can ruin the entire performance. Since most supply chains are optimized for efficiency, there is not much room for significant errors, which are magnified in the stretched, globalized supply chains that we have today. The current bottleneck situation at the Southern California port is emblematic of what can go wrong if a carefully choreographed system of moving goods is stretched beyond its capacity.
When, and how, can this crisis be resolved?
It is difficult to predict exactly when this will be resolved, especially given that we are not out of the woods yet with COVID. I hope we will have a better view after the holiday season has passed. My guess is that the demand-supply imbalance will persist well into next year, long after the current bottleneck situation at the ports is resolved.
What’s unique about the “Big Crunch” we are witnessing today is that disruptions have occurred on both supply and demand sides. Products are not being made and delivered in time because of plant closures and labor shortages; at the same time, demands for some products have exploded while others have tanked. Rarely have we seen such major disruptions occurring simultaneously.
The last big supply-chain disruption occurred in 2011 after the Tohoku earthquake in Japan, which shut down global supply of electronics and auto parts for weeks. At that time, there was a scramble to satisfy unfilled demands, but the demand itself was unperturbed, unlike what is happening now.
In addition, pandemic-induced disruptions have been occurring in a prolonged, phased, and unlocalized manner. As COVID hit different parts of the world in waves, a production shutdown in one place was followed by another in a different place, then by another, and so on. This has created a previously unforeseen dynamic in which a bottleneck shifted constantly around different corners of supply chains, leaving managers with extremely limited maneuverability. As a result, many recovery attempts at local levels turned out to be short-lived.
At some point, all of these disturbances will settle down, although it may take a while. Companies have adjusted their sourcing and logistics options and introduced new ways to get around the issues. For example, reliance on air freight has increased because of driver unavailability. While there are obvious cost implications, companies may have discovered that the advantage of a fast and reliable shipping option may outweigh the downsides, at least for transporting certain goods.
Similarly, it has been reported that the supply-chain crisis also accelerated the movement toward autonomous vehicle development. As an academic, I am curious to find out how much of these new practices will stick and what the “new normal” will look like. In my mind, there is no doubt that some of the established notions that guided years of supply-chain practices will be revised or replaced.
How can the supply chain be run better to avoid this, and who and what would that involve?
A playbook for mitigating the impact of supply-chain disruptions exists, although its effectiveness has been uneven during the pandemic.
In broad terms, there are two categories of mitigation strategies: duplication and flexibility. Duplication means organizations create redundancies in their resources and assets, such as safety stock of inventories and secondary suppliers. These extra resources help reduce the impact of disruptions when they occur. However, they are typically very expensive to install and maintain—safety stocks unused during normal times tie up capital, and establishing a relationship with secondary suppliers requires big investments.
The problem becomes even more pronounced when the disruptions are rare and unpredictable, like the ones induced by natural disasters or the pandemic. Building flexibility, such as rerouting production capacity to certain goods at the expense of others, is a more cost-effective solution, but its usefulness is bounded by the existing setup for producing and delivering goods.
Some companies used these strategies better than others during the pandemic. However, because the nature of disruptions was so unique, as mentioned above, it is safe to say that no one was prepared for what ended up happening. One of the lessons we’ve learned—which is not new, but whose importance has become heightened—is that a coordinating mechanism is sorely lacking in today’s supply chains. In their race to get their items on retailer shelves on time, competing firms inflated their forecasts and strained supply chains more than necessary. A normal functioning of a “common good” resource such as port capacity suffered as a result.
Especially for managing the flow of products with public health or national strategic importance, like PPE, perhaps it is time to start a conversation about the government providing a “control tower” role that would address blind spots that exist in the current decentralized global supply chain networks, involving such activities as gathering and disseminating data on the availability of raw materials and their dependency across different sectors.